Your core business: manufacturing. Our mission: the smooth running of your manufacturing processes. That’s why we always tailor our maintenance strategy to your company's specific needs. Our experts are there to help you with preventative maintenance and repairs.
Production Equipment Maintenance
Customised maintenance strategies from Leadec
We know that production facilities that run smoothly are the success factor for your company. Everything must work without any problems! Whether repairs, inspection, or preventative maintenance, our maintenance strategies for your company increase the service life of your plant and equipment, minimising the risk of downtime. What sets us apart is our employees. Thanks to extensive know-how, the highest operational safety and quality assurance standards, and close cooperation with our customers, we are the ideal partner for all questions concerning factory maintenance.
Our promise: We take care of your plant and equipment so that you can concentrate on your core business.
Our services in Production Equipment Maintenance
Inspection and preventative maintenance
- Creation of a maintenance schedule in the customer’s or Leadec’s own CAFM system
- Creation of an optimised maintenance regime aligned with statutory requirements, technical standards, overall equipment effectiveness (OEE) and best value
- Online/offline maintenance according to existing production planning
- Mobile documentation of defects and activities
- Optimisation of maintenance schedules through evaluation of fault events
Breakdown analysis
- Extensive data acquisition with monitoring and reporting systems
- Regular evaluation on the basis of technical and commercial criteria
- Identification of weak points and trouble spots
- Initiation of countermeasures and technical improvements
- Individual adjustment of maintenance schedules, spare parts storage, or processes
Optimisation and overhaul of machinery
- Modification and expansion of existing machines and facilities
- General overhaul, modernisation, and retrofit of existing facilities
- Optimisation to increase dependability
- Data-driven asset lifecycle modelling and replacement/refurbishment programme planning
Workshop management
- Inspection, overhaul and repair of assemblies, spare parts, and operating equipment
- Transparent order management and item identification
- Standardisation of processes to reduce throughput times
- Execution in a framework agreement, according to the offer or as an immediate service
- Logistics service
Tool management
- Disposition and procurement of tools and clamping devices, independent of suppliers
- Tool setting at the customer’s or at our own site
- Logistics and transport of the adjusted tools directly to the production line
- Tool storage in the customer’s or our own tool crib
- Process engineering for continuous tool and cost optimisation
IT services
- Digital equipment data collection for status and quantity recording
- Leadec.os – comprehensive ERP system for all maintenance services
- Process data acquisition for condition monitoring and quality assurance
- Remote service with video support
- Complete documentation according to legal requirements
Planned and corrective maintenance
- Monitoring of plant and equipment for shortest possible response times and early warning of potential faults, so intervention can be scheduled to prevent rather than react to breakdown
- Tracking of messages, alerts, and activities in the ticket system
- Immediate repair in shift operation or on call
- Repair of various production facilities, storage, and conveyor systems, as well as production-related systems
- Immediate reporting and coordination of further steps with production, quality assurance, and HSQE managers
- Creation of digital machine manuals for fast troubleshooting and repair
- Use of state-of-the-art measuring and analysis equipment for the identification of sporadic, minor faults
- Detailed planning of non-time-critical repairs
TPM and shop floor management
- Comprehensive integration of a total productive maintenance (TPM) system
- Ensuring the availability of equipment in the production environment
- Qualification of personnel for maintenance tasks according to requirements
- Extensive reporting of key figures on visualisation boards
- Regular team meetings with all employees
- Participation in customer meetings for communication at eye level
Regulatory inspections
- Tests according to applicable rules, standards, and laws
- Inspection of safety devices, machines, systems, and operating equipment
- Review of safety-relevant documentation
- Direct repair of defects
- Message to the operator with recommended action
Spare parts management
- Review of system documentation and recording of installed components
- Selection of spare parts and recommendation for customer’s warehouse
- Critical parts analysis, stockholding, and management
- Procurement and provision of spare parts by Leadec
- Inventory optimisation of existing warehouses
- Presentation of alternatives such as spare parts sharing and additive manufacturing
- Inventory management in the customer’s or Leadec’s own ERP system
- Logistics strategies for procurement and storage
- Obsolescence management
Fluid management
- Monitoring and logistics for water-soluble and oil-based metalworking fluids
- Walk-throughs for inspecting, sampling, and refilling decentralised MWF systems
- Coordination of samples and documentation of laboratory results
- Immediate measures in case of limit violations and analysis of long-term trends
- Suggestion of recommended action
- Execution of coordinated measures
- Cleaning of tanks and equipment
- Operation of tank farms, dosing, and mixing systems
- Service for lubricants, as well as gear and hydraulic oils
- Professional and environmentally-compliant disposal of all liquids
Your advantages
- Reduction of downtime: We ensure that facility downtimes are minimised and recorded.
- Cost reduction: We effectively reduce costs through high work efficiency, careful planning, preventative measures, and continuous optimisation.
- High degree of safety: Our services are certified to ISO:45001 to ensure high operational safety and quality assurance.
- Transparent documentation: We show the facility’s weak points, document the actual state, and present important key figures.
- Stock optimisation: We optimise your company’s inventory and thus reduce tool and storage costs.
- Value retention of plant and equipment: We ensure an optimised service life of plant and machinery, and thus continuously improve performance.
- Predictive maintenance: Increased plant availability through early detection of damage or warning of potential failure.
- Sustainable measures: Thinking about tomorrow today with Leadec’s environmentally-friendly maintenance strategy.
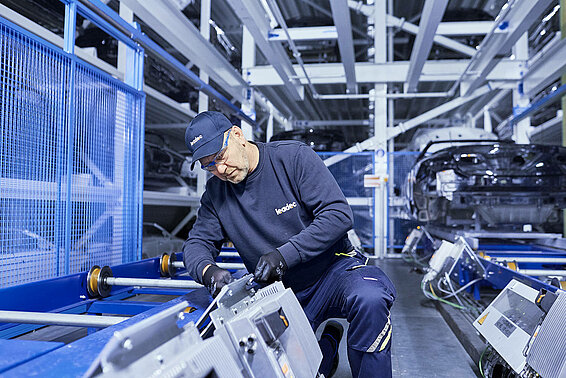
Digital solutions for Production Equipment Maintenance
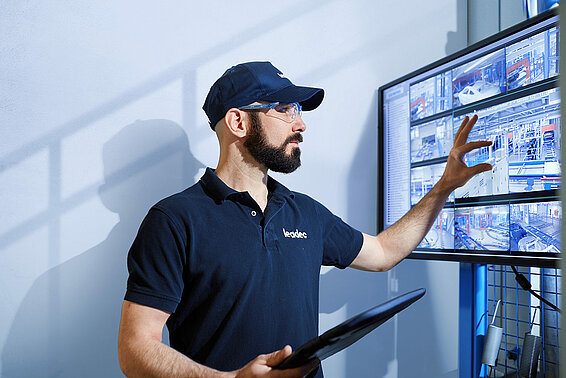
With our digital offer, we provide transparency and increased service quality. Suitable for every service, these solutions optimally complement production maintenance.
Smart Condition Monitoring
With Smart Condition Monitoring, we not only provide preventative maintenance, but also intelligent condition monitoring. In three phases, we detect anomalies, install sensors or IT systems, and finally define intelligent guidelines for action.
Looking to connect with us?
Write us a message or set up an online Teams appointment with your local representative.
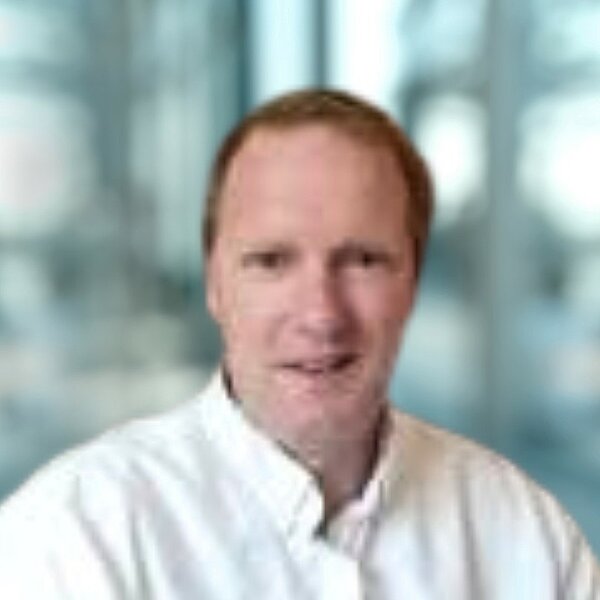